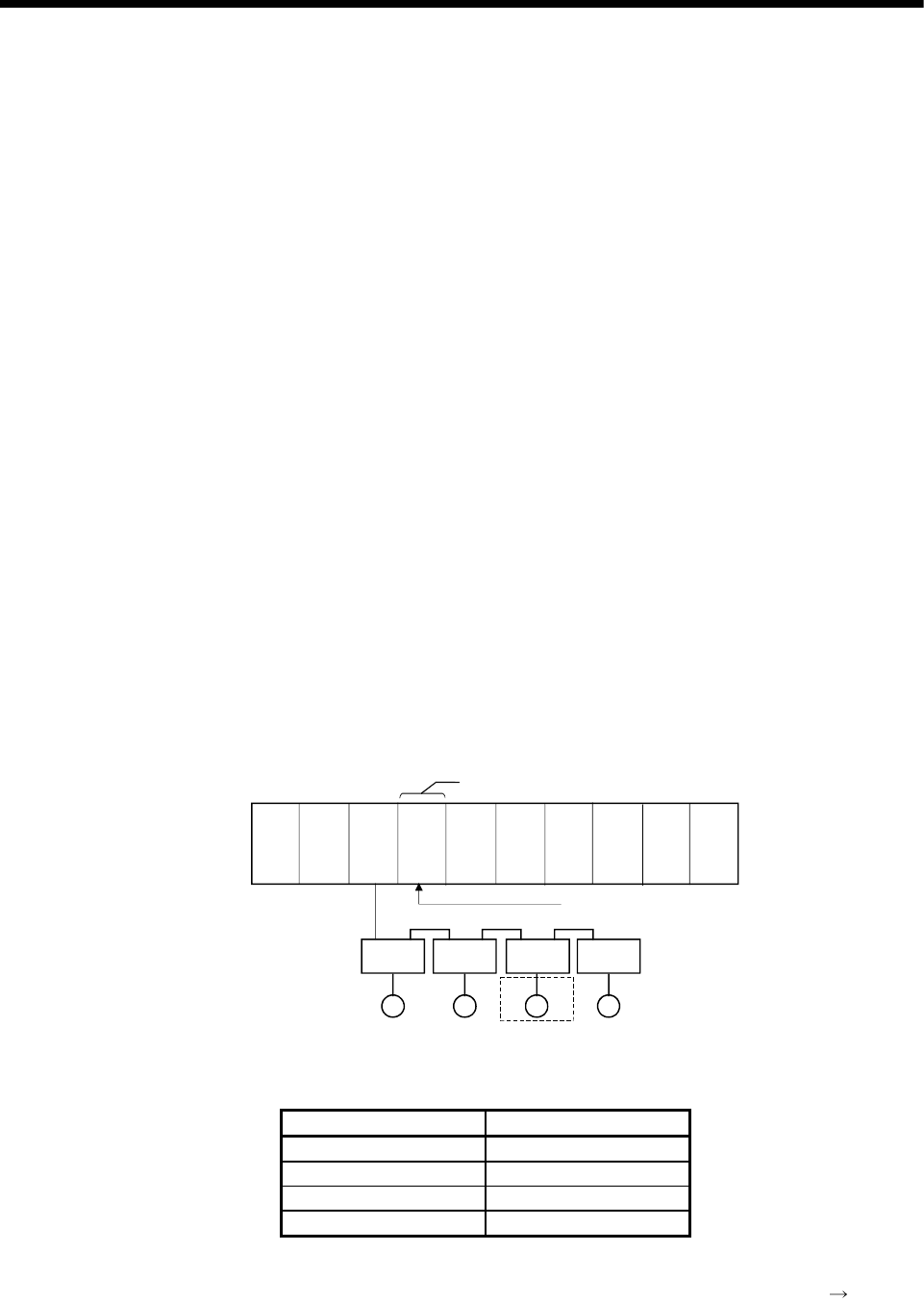
6 -
160
6 POSITIONING CONTROL
[Cautions]
(1) Number of control axes is 1 axis.
(2) Only the absolute data method (ABS) is used for positioning control to the pass
points.
(3) The speed can be changed during the start.
The changed speed is effective until the stop command is input.
(4) Set the positioning address in the servo program using indirect setting with the
word devices D, W and #.
(5) Use only even-numbered devices for indirect setting of positioning address in the
servo program.
If odd-numbered devices are used, an error [141] occurs at the start and control
does not start.
(6) Positioning speeds can be set in the servo program using indirect setting with the
word devices D, W and #.
However, this data is effective only at the position follow-up control start (servo
program start) and the speed does not change if the indirect setting are changed
during the start.
[Program]
(1) System configuration
Axis 3 position follow-up control for PLC CPU (CPU No.1) to Motion CPU (CPU
No.2).
MM MM
PLC CPU control module
Positioning start command : X0
(PLC CPU device)
Axis
4
Axis
1
Axis
2
Axis
3
AMP AMP AMP AMP
Q61P Q02H
CPU
Q172H
CPU
QX41
(2) Positioning conditions
(a) Position follow-up conditions are shown below.
Item Setting
Servo program No. 100
Control axis Axis 3
Positioning address D4000
Positioning speed 20000
(b) Position follow-up control start command
..............................................................Turning X0 off to on (OFF
ON)
(PLC CPU device)