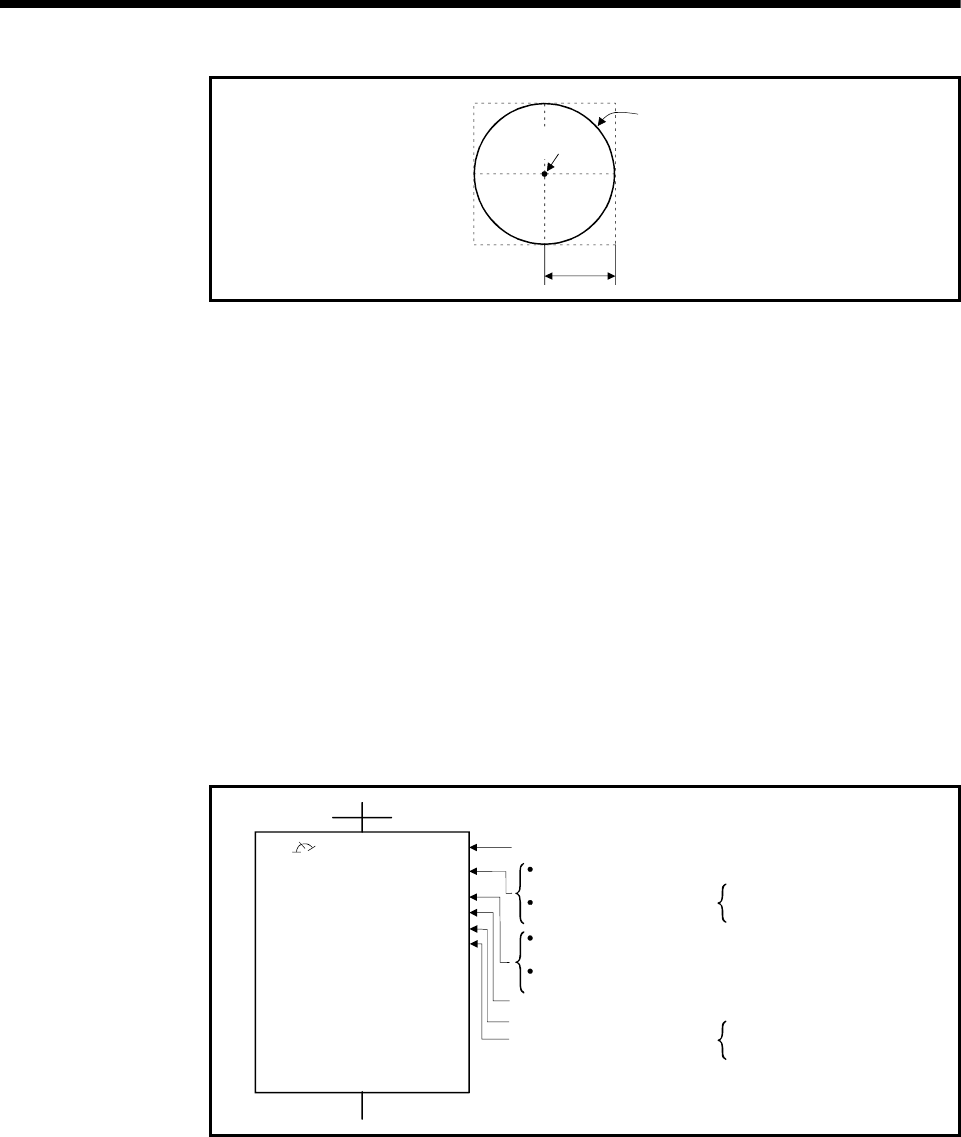
6 - 75
6 POSITIONING CONTROL
Maximum arc
2
31
-1-2
31
2
31
-1
0
Radius R
Arc central point
(4) Set the command speed with the combined-speed for 2 axes circular interpolation
axis.
(5) The command speed unit is specified in the parameter block.
(6) Set the number of pitches within the range of 0 to 999. If it is set outside the
setting range, the servo program error [28] occurs and operation does not start.
(7) All of the circular interpolation axis, linear axis end point address, command
speed, radius (2 word data above), and number of pitches (1 word data) are set
indirectly by D, W and #.
[Program]
(1) Servo program
Servo program No.61 for incremental auxiliary point-specified helical interpolation
control is shown below.
<K 61>
INH
Axis
Axis
Linear axis
Speed
Number of pitches
Auxiliary point
Auxiliary point
1,
2,
3,
1,
2,
88541
30000
20000
1000
500
45000
20000
Axis for the circular . . . . . . . .
interpolation
End point relative address from . . . . . . . . . 20000
the linear axis specification
Positioning speed . . . . 1000
Number of pitches . . . .
Auxiliary point relative . . . . . . . .
address of the arc
Axis 1 . . . . 88541
Axis 2 . . . . 30000
Linear axis for the circular . . . . . . . . . . . . . Axis 3
interpolation and linear interpolation
End point relative address of
the circular interpolation axis
500
Axis 1, Axis 2
Axis 1 . . . . 45000
Axis 2 . . . . 20000
Incremental auxiliary point-specified circular helical interpolation
(Note): Example of the Motion SFC program for positioning control is shown next page.