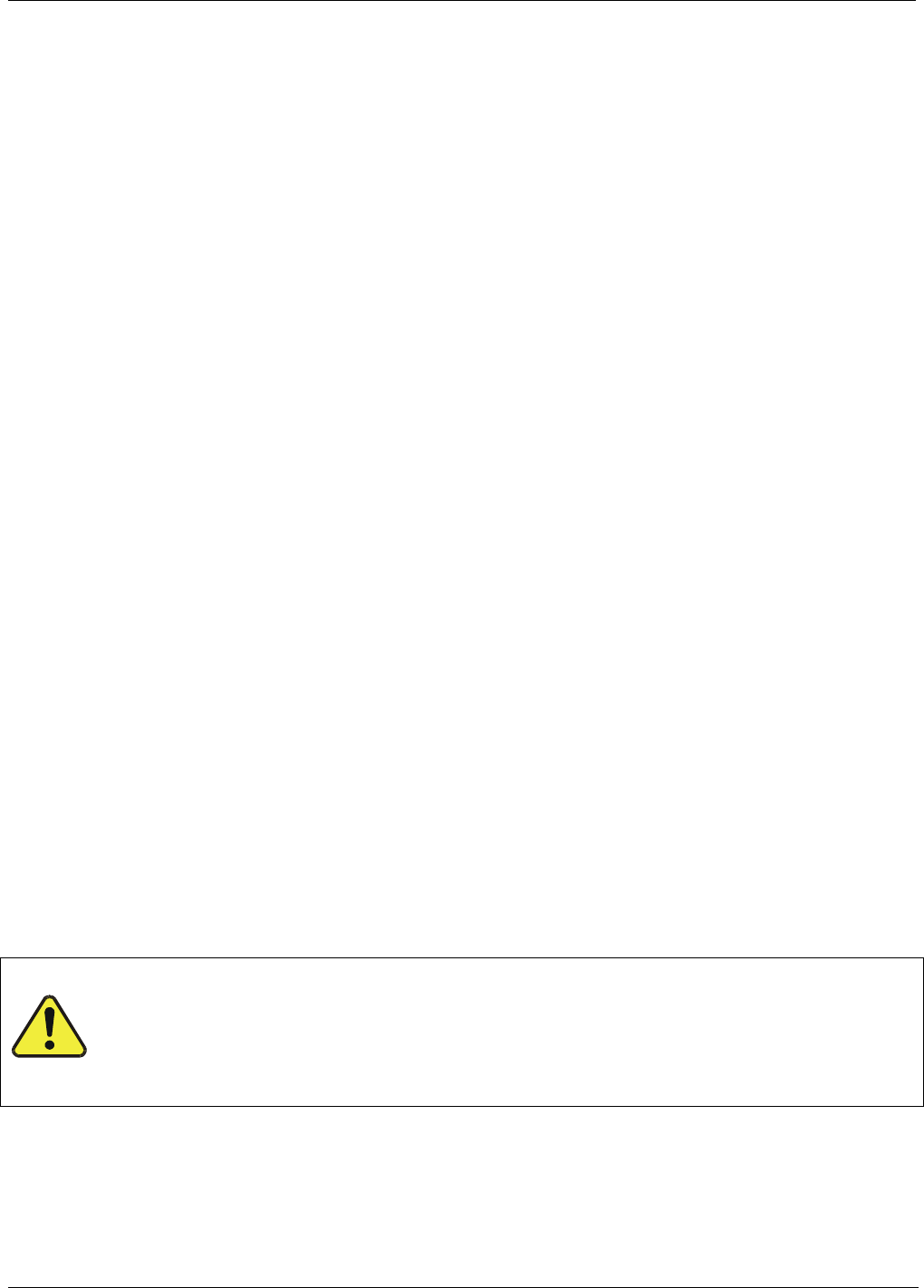
Instrument Maintenance T400 Ozone Analyzer Operator’s Manual
232
11.3.4. IZS DESICCANT (OPTION 56)
The M400E can be fitted with a desiccant dryer to provide a dry air source to the IZS
sub-system. This option consists of a rear panel mounted scrubber cartridge filled with
anhydrous calcium sulfate (CaSO4) desiccant.
The desiccant material is expendable and must be replaced at regular intervals.
The material exhibits a color change when it has been saturated with water vapor,
turning from blue to pink.
The scrubber cartridge should be refilled before the entire scrubber turns pink.
Replacement interval will depend on how often the IZS is used, as well as ambient
levels of humidity in your application.
Initially the desiccant should be frequently monitored until a standard replacement
interval can be established.
11.3.5. PERFORMING LEAK CHECKS
Leaks are the most common cause of analyzer malfunction; Section 11.3.5.1 presents a
simple leak check procedure. Section 11.3.5.2 details a more thorough procedure.
11.3.5.1. Vacuum Leak Check and Pump Check
This method is easy and fast. It detects, but does not locate most leaks; it also verifies
that the sample pump is in good condition.
1. Turn the analyzer ON, and allow enough time for flows to stabilize.
2. Cap the sample inlet port.
3. After 2 minutes, when the pressures have stabilized, note the SAMP FL and PRES
test function readings on the front panel.
4. If SAMP FL < 10 CC/M then the analyzer is free of any large leaks.
5. If PRES < 10 IN-HG-A then the sample pump diaphragm is in good condition.
11.3.5.2. Pressure Leak Check
If you cannot locate the leak by the above procedure, obtain a leak checker similar to the
TAPI part number 01960, which contains a small pump, shut-off valve and pressure
gauge. Alternatively, a tank of pressurized gas, with the two-stage regulator adjusted to
≤ 15 psi; a shutoff valve and pressure gauge may be used.
CAUTION – General Safety Hazard
Once the fittings have been wetted with soap solution, DO NOT apply / re-apply
vacuum, as this will cause soap solution to be drawn into the instrument,
contaminating it.
DO NOT exceed 15 psi pressure.
1. Turn OFF power to the instrument.
2. Install a leak checker or tank of gas as described above on the sample inlet at the
rear panel.
3. Install a cap on the exhaust fitting on the rear panel.
06870C DCN6332