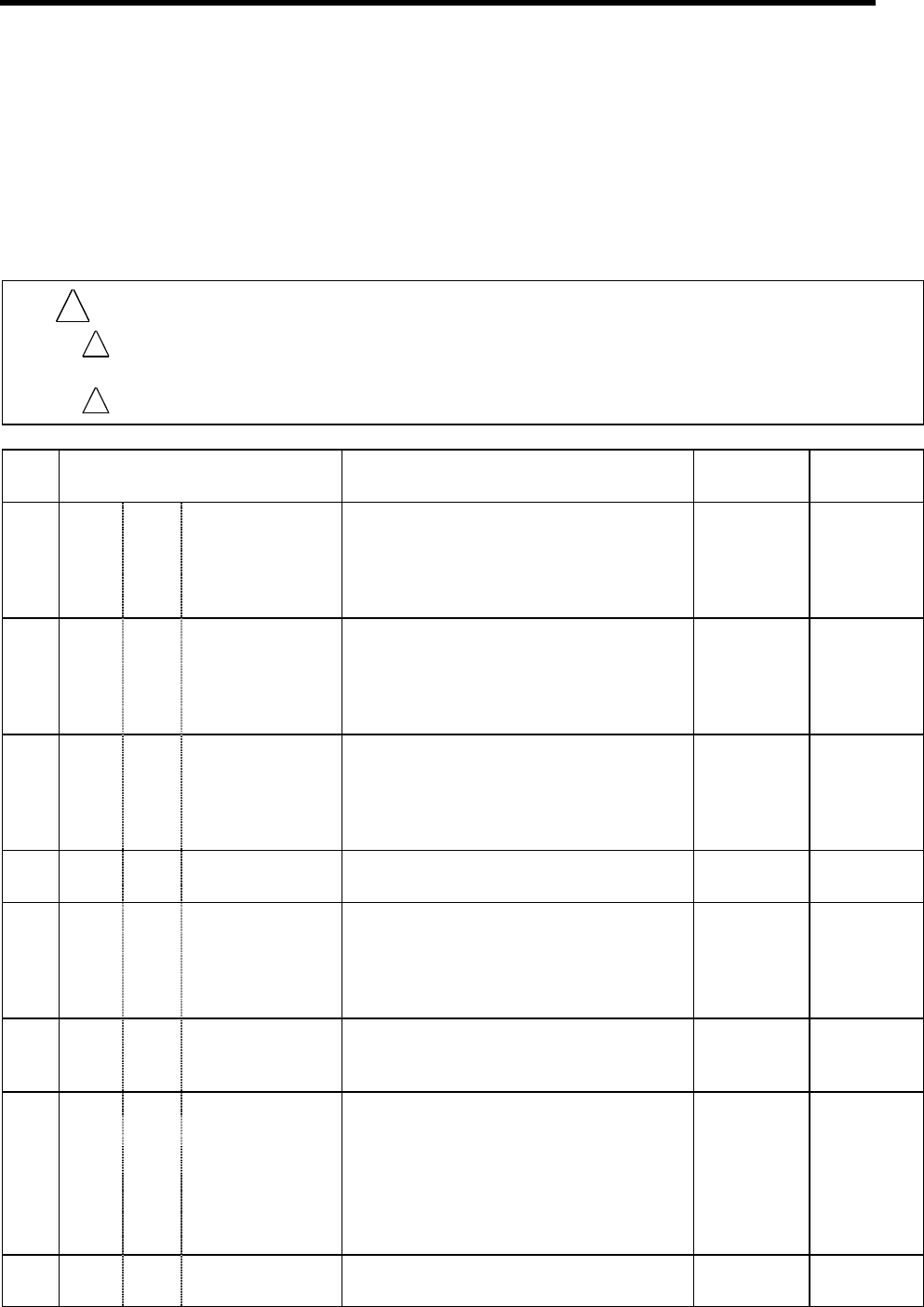
8. Spindle Parameters
8.4 MDS-C1-SPM
234
8.4 MDS-C1-SPM
The spindle parameter setting and display method will differ according to the NC being used, so refer to
Instruction Manual for each NC and the following spindles.
MELDAS AC Servo and Spindle MDS-C1 Series Specifications Manual ........................BNP-C3000
For parameters marked with a (PR) in the tables, turn the NC power OFF after setting. The parameters
will be valid after the power is turned ON again.
The "fixed control constants" and "fixed control bits" in this section are set by Mitsubishi.
!
CAUTION
!
Do not make remarkable adjustments or changes of the parameters as the operation may
become unstable.
!
In the explanation on bits, set all bits not used, including blank bits, to “0”.
No. Items Details
Setting
range
Standard
setting
3201 SP001 PGM Magnetic sensor
and motor built-in
encoder
orientation
position loop gain
As the set value is larger, the orientation
time becomes shorter and servo rigidity is
increased.
However, vibration is increased and the
machine becomes likely to overshoot.
0 to 2000
(0.1 1/s)
100
3202 SP002 PGE Encoder
orientation
position loop gain
As the set value is larger, the orientation
time becomes shorter and servo rigidity is
increased.
However, vibration is increased and the
machine becomes likely to overshoot.
0 to 2000
(0.1 1/s)
100
3203 SP003 PGC0 C-axis non-cutting
position loop gain
Set the position loop gain in C-axis
non-cutting mode.
During non-cutting (rapid traverse, etc.)
with the C axis control, this position loop
gain setting is valid.
1 to 200
(1/s)
15
3204 SP004 OINP Orientation
in-position width
Set the position error range in which an
orientation completion signal is output.
1 to 2880
(1/16 °)
16
3205
(PR)
SP005 OSP Orientation mode
changing speed
limit value
Set the motor speed limit value to be used
when the speed loop is changed to the
position loop in orientation mode.
When this parameter is set to "0", SP017
(TSP) becomes the limit value.
0 to 32767
(r/min)
0
3206 SP006 CSP Orientation mode
deceleration rate
As the set value is larger, the orientation
time becomes shorter. However, the
machine becomes likely to overshoot.
1 to 1000 20
3207 SP007 OPST In-position shift
amount for
orientation
Set the stop position for orientation.
(i) Motor built-in encoder, encoder:
Set the value by dividing 360° by
4096.
(ii) Magnetic sensor:
Divide –5° to +5° by 1024 and put
0° for 0.
(i) 0 to 4095
(ii) –512 to
512
0
3208
SP008 Not used. Set to "0". 0 0