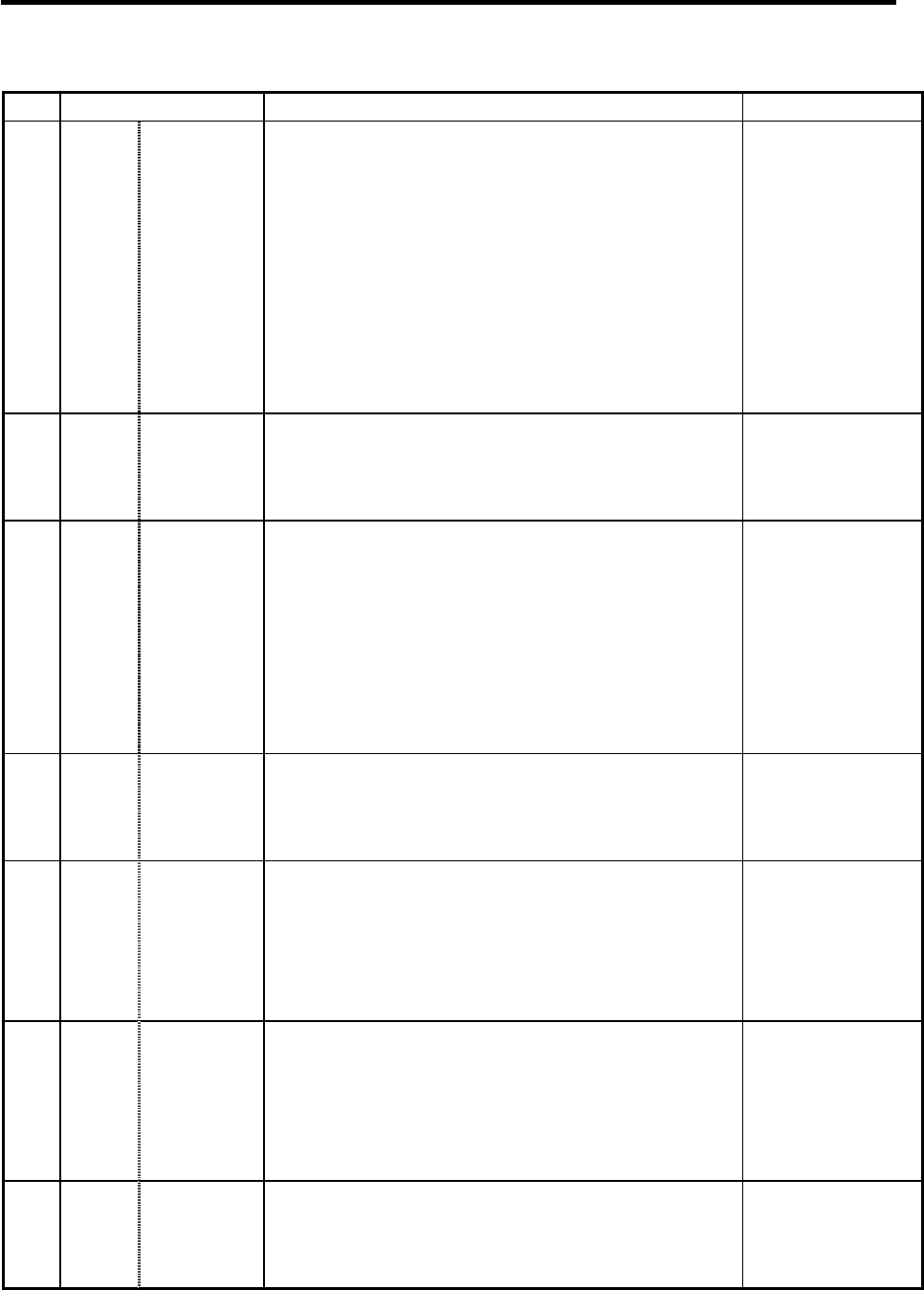
5. Base Specifications Parameters
39
# Items Details
Setting range (unit)
1193 inpos Validate
in-position
check
Specify the deceleration confirmation method for the
positioning command.
0: Command deceleration check
(Positioning is completed when the deceleration
is completed with the acceleration/deceleration
speed issued from the control unit.)
1: In-position check
(Positioning is completed by detecting that the
servo amplifier has reached within a set distance
from the end point. The set distance is set in
"#2224 SV024".)
0: Command
deceleration
check
1: In-position
check
1194 H_acdc Time
constant 0
for handle
feed
Specify the time constant for the manual handle feed.
0: Use time constant for G01
1: Time constant 0 (step)
0/1
1195
1196
1197
1198
Mmac
Smac
Tmac
M2mac
Macro call for:
M command
S command
T command
Second
miscellaneous
code
Specify the user macro M‚ S or T command macro call
out.
Macro call out with M command
Macro call out with S command
Macro call out with T command
Macro call out with 2nd miscellaneous command
0: Invalid
1: Valid
1199
(PR)
Sselect Select initial
spindle
control
Select the initial condition of spindle control after power
is turned on.
0: 1st spindle control mode (G43.1)
1: 2nd spindle control mode (G44.1)
0: G43.1
1: G44.1
1200
(PR)
G0_acc
Validate ac-
celeration and
deceleration
with inclination
angle constant
G0
Set up acceleration and deceleration types when a
rapid traverse command is issued
0: Acceleration and deceleration (conventional) with
time constant
1: Acceleration and deceleration with inclination
angle constant
0/1
1201
(PR)
G1_acc
Validate ac-
celeration and
deceleration
with inclination
constant
G1
Set up acceleration and deceleration types when a liner
interpolation command is issued.
0: Acceleration and deceleration (conventional) with
time constant
1: Acceleration and deceleration with inclination
angle constant
0/1
1202 mirofs
(For L
system
only)
Distance
between
facing turrets
Set up the distance between tools (noses) (between
turrets).
0 to 99999.999
(mm)