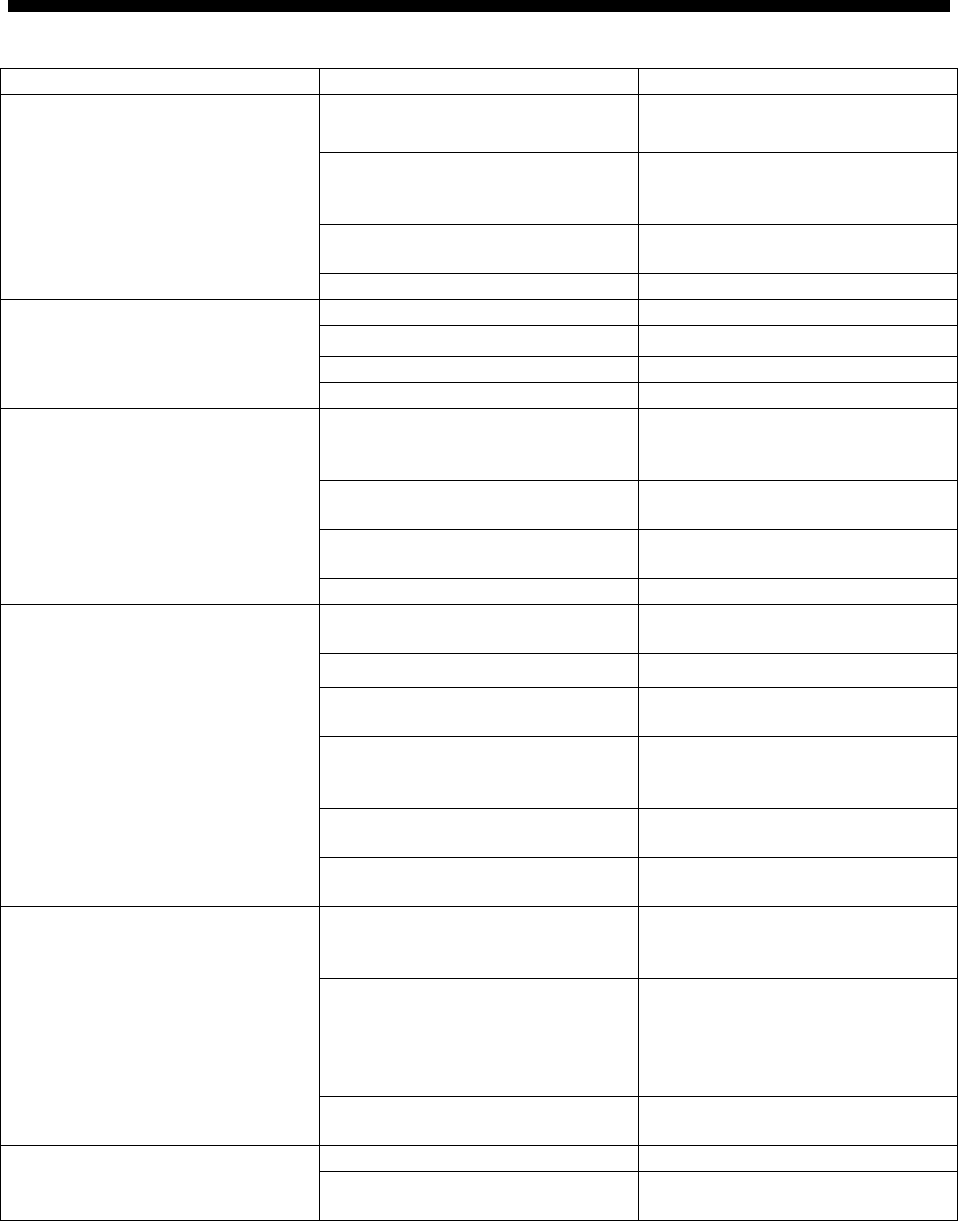
2–Pump 20-Station Controllers Troubleshooting 43 of 51
Chapter 7: Troubleshooting
7-1 General Troubleshooting
Problem Possible Cause Solution
The control panel is not turned on. Turn on the control panel.
The external disconnect
(recommended) in the dedicated
circuit is open (off).
Close the switch (on).
Fuse/circuit breaker in the power
drop is blown/tripped.
Replace/reset.
The control panel doesn’t light up at
all
Control power switch is broken. Replace.
Fuse in display is blown. Replace.
Loose wiring to display. Repair.
Power supply problem. Check 24V DC source.
The touch screen display doesn’t
come on when the control panel is
powered up.
Display is faulty. Replace.
The motor overload has tripped. Reset the overload and check the
motor for the proper amp draw on
tag.
Hoppers not assigned/no demand. Check hopper assignment, verify
hoppers are online.
Main fuse in power drop or optional
fused disconnect has blown.
Replace the fuse.
A pump package doesn’t run, even
though it is on-line and its indicator
is lit.
Motor contact is faulty. Repair or replace as required.
The hopper is off-line. Use the controller to put the vacuum
receiver on-line.
Faulty level sensor or loose. Check level sensor/wiring.
The convey time for the hopper is
set to zero.
Use the controller to enter a longer
convey time.
The field-installed station bypass
switch is simulating a Bin Full
condition.
Normal operation. Set the switch so
the vacuum receiver is back in the
loading sequence.
The field-installed station bypass
switch is bad or mis-wired.
Repair, replace, or re-wire.
A vacuum receiver is being by-
passed in the loading cycle.
The vacuum receiver was assigned
to the wrong pump during setup.
Repeat the setup procedure and
verify that the pump is on.
Conveying times are too long (Time
Fill Mode only).
Time the vacuum receiver (s) during
loading, and set the conveying times
to a few seconds less.
Maximum conveying times are too
long, and the PLC does not
recognize the Vacuum Receiver Full
Proximity Switch(es).
Check proximity sensors for proper
operation and proper wiring to the
PLC. Repair as needed. Reset the
conveying times to a reasonable
value, and adjust as needed.
Vacuum hoppers are overfilling.
Special convey is enabled and
convey time is too long.
Disable special convey. Reduce
convey time.
Check PLC. See if fault light is on. Reload software. See page 43. Power is present but control will not
function.
Loose communication cable between
PLC and display
Verify wiring.