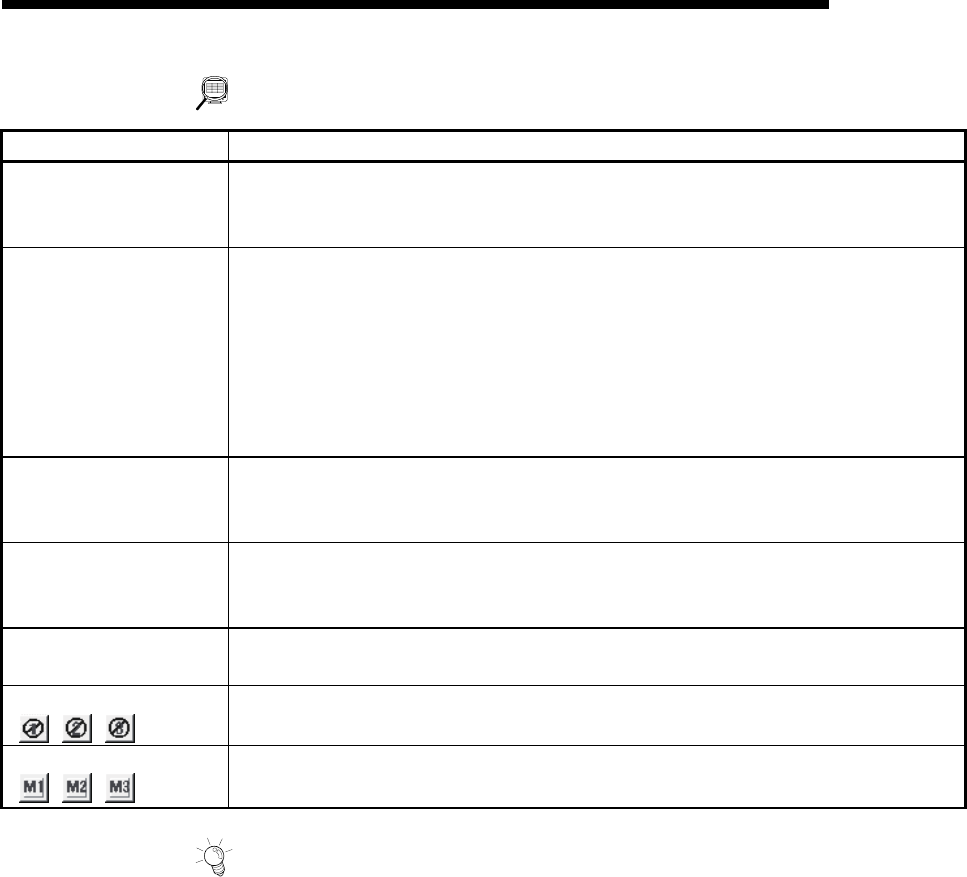
11 - 37 11 - 37
MELSOFT
11. POSITIONING DEBUGGING
DISPLAY/SETTING DATA
Item Description
Return Method
OPR
Creep speed
Shows the values set to the OPR basic parameters and OPR extended parameters.
Refer to Section 8.1.5 for the setting of the OPR basic parameters.
Refer to Section 8.1.6 for the setting of the OPR extended parameters.
OPR return Method
Choose the type of the starting method used in the OPR test.
• Mechanical OPR
OPR is made using the DOG signal or zero signal according to the OPR return method.
Executed to set up the original point.
• Rapid OPR
Operation of positioning to the original point is performed in the travel distance calculated
from the mechanical feed distance and the original point address set to the OPR basic
parameters after the original point has been set up.
"#1 req." button
"#2 req." button
"#3 req." button
Click any button to start OPR set to OPR return Method.
"#1 stop" button
"#2 stop" button
"#3 stop" button
Click the corresponding button to stop the axis returning to the original point.
Reset the error after a stop since the axis results in an error occurrence status.
"All stop" button
Click this button to stop all operating axes.
Reset the error after a stop since the axis results in an error occurrence status.
"Error reset" button
(
/
/ )
Click any button to reset the error of the corresponding axis.
"M code Off" button
(
/
/ )
Click any button to turn off the M code ON signal (XD, XE, XF) of the corresponding axis.
HELPFUL OPERATION
Use the following operation example to set up the original point when the OPR
method is the count type #2.
1. Perform steps 1 to 3 of the basic operation.
2. Click the "Operation" button on the operation monitor main screen.
3. Click the <<OPR monitor>> tab in the Operation Monitor dialog box.
4. Click the "Ope. Test" button in the Operation Monitor dialog box.
5. Click the <<OPR>> tab in the Test data set dialog box.
6. Make the OPR test in the Mechanical OPR method.
7. If the position defined as the original point in the OPR test is different from the
planned position, perform JOG operation to measure the error.
Refer to Section 11.2.6 for JOG operation.
8. Correct the error to the travel distance after DOG in the OPR extended
parameters.
Refer to Section 8.1.6 for the setting of the OPR extended parameters.