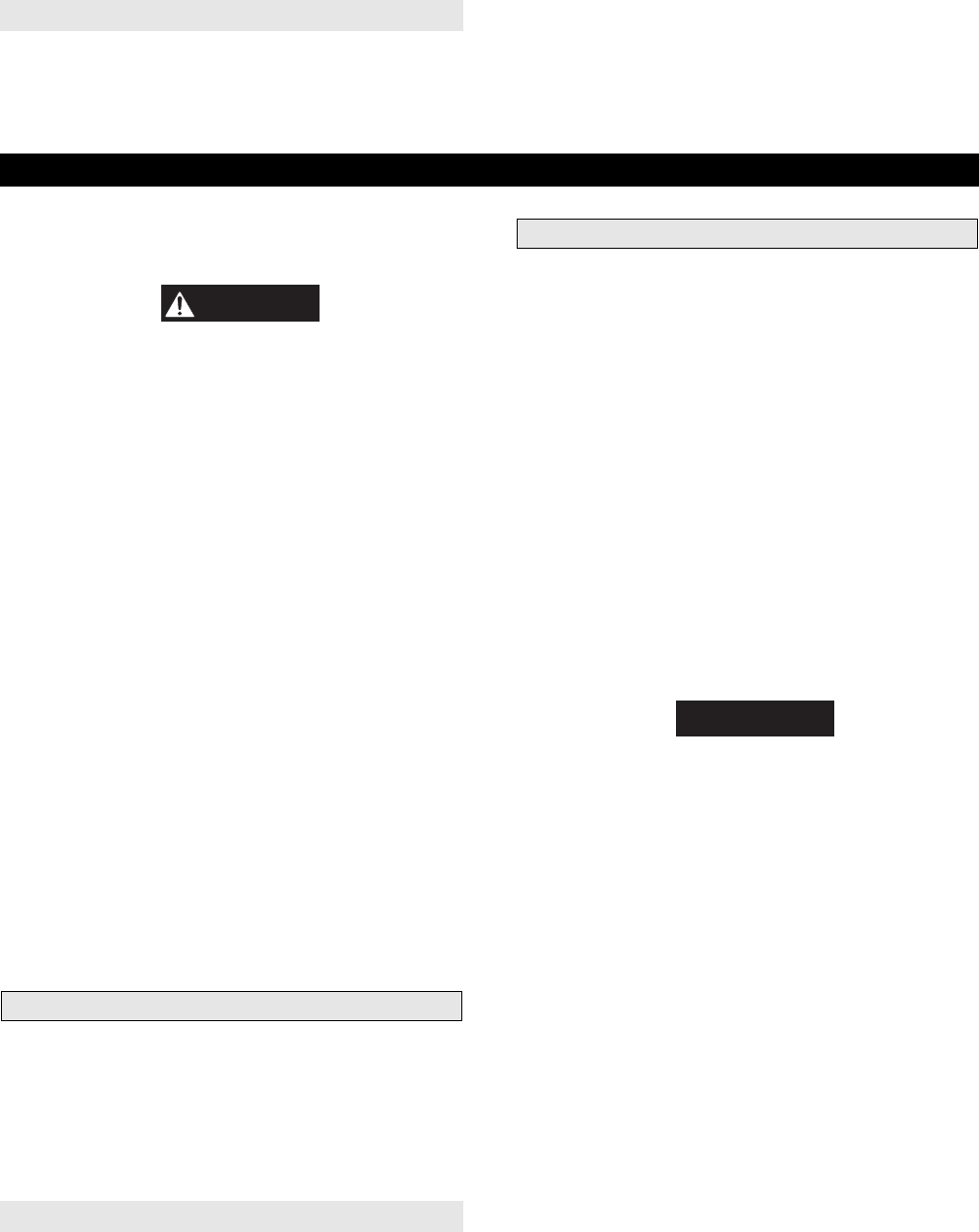
MHD56037 - Edition 5 21
Drum Locking Pin (optional feature)
Refer to Dwg. MHP0155 on page 61.
Lubricate at least once every month, depending on environment
and duty cycle, through grease fitting (139) located in gland (138)
with 2 or 3 pumps of a grease gun.
If drum locking pin is disassembled, clean all parts thoroughly
and coat with clean grease. Refer to ‘Recommended Lubricants’
section. Use sufficient grease to provide a good protective coat.
Lubrication will help to prevent rust and allow easier locking pin
operation.
INSPECTION
Inspection information is based in part on American Society of
Mechanical Engineers Standards Safety Codes (ASME B30.7).
WARNING
• All new or repaired equipment should be inspected and
tested by personnel instructed in safety, operation and
maintenance of this equipment to ensure safe operation at
rated specifications before placing equipment in service.
• Never use a winch that inspection indicates is damaged.
Frequent and periodic inspections should be performed on
equipment in regular service. Frequent inspections are visual
examinations performed by operators or personnel trained in
safety and operation of this equipment and include observations
made during routine equipment operation. Periodic inspections
are thorough inspections conducted by personnel trained in safety,
operation and maintenance of this equipment. ASME B30.7 states
inspection intervals depend upon the nature of critical
components of the equipment and severity of usage. The
inspection intervals recommended in this manual are based on
intermittent operation of winch eight hours each day, five days
per week, in an environment relatively free of dust, moisture, and
corrosive fumes. If winch is operated almost continuously, or
more than eight hours each day, more frequent inspections will be
required.
Careful inspection on a regular basis will reveal potentially
dangerous conditions while still in the early stages, allowing
corrective action to be taken before condition becomes dangerous.
Deficiencies revealed through inspection, or noted during
operation, must be reported to designated personnel instructed in
safety, operation and maintenance of this equipment.
A determination as to whether a condition constitutes a safety
hazard(s) must be decided, and correction of noted safety
hazard(s) accomplished and documented by written report before
placing equipment in service.
Records and Reports
Inspection records, listing all points requiring periodic inspection
should be maintained for all load bearing equipment. Written
reports, based on severity of service, should be made on condition
of critical parts as a method of documenting periodic inspections.
These reports should be dated, signed by the person who
performed inspection, and kept on file where they are readily
available for authorized review.
Wire Rope Reports
Records should be maintained as part of a long-range wire rope
inspection program. Records should include the condition of wire
rope removed from service. Accurate records will establish a
relationship between visual observations noted during frequent
inspections and actual condition of wire rope as determined by
periodic inspections.
Frequent Inspection
On equipment in continuous service, frequent inspection should
be made by operators at the beginning of each shift. In addition,
visual inspections should be conducted during regular operation
for indications of damage or evidence of malfunction (such as
abnormal noises).
1. WINCH. Prior to operation, visually inspect winch housings,
controls, brakes, side rails and drum for indications of
damage. Do not operate winch unless the wire rope feeds
onto drum smoothly. Any discrepancies noted must be
reviewed and inspected further by authorized personnel
instructed in operation, safety and maintenance of this winch.
2. WIRE ROPE. Visually inspect all wire rope which can be
expected to be in use during the day’s operations. Inspect for
wear and damage indicated by distortion of wire rope such
as kinking, “birdcaging,” core protrusion, main strand
displacement, corrosion, broken or cut strands. If damage is
evident, do not operate winch until the discrepancies have
been reviewed and inspected further by personnel
knowledgeable on wire rope safety and maintenance
procedures.
NOTICE
• The full extent of wire rope wear cannot be determined by
visual inspection. At any indication of wear inspect wire rope
in accordance with instructions in “Periodic Inspection.”
3. AIR SYSTEM. Visually inspect all connections, fittings,
hoses and components for indication of air leaks. Repair any
leaks or damage.
4. PENDANT (optional feature). Ensure operation of pendant
levers is smooth and winch is responsive to pendant control.
Pendant levers must spring return to the neutral position
when released.
5. MANUAL THROTTLE LEVER. Ensure operation of
manual throttle lever is smooth and winch is responsive to
lever movement. Lever must return to neutral and lock in
place when released. If winch responds slowly or controls
stick, do not operate winch until all problems have been
corrected.
6. BRAKES. During winch operation test brakes. Brakes must
hold load without slipping. Automatic brakes must release
when winch motor throttle is operated. If brakes do not hold
load, or do not release properly, brakes must be adjusted or
repaired.
7. WIRE ROPE REEVING. Check reeving and ensure wire
rope is properly secured to the drum. Do not operate winch
unless wire rope feeds onto drum smoothly.
8. LUBRICATION. Refer to “LUBRICATION” section for
recommended procedures and lubricants.
9. LIMIT SWITCHES (optional feature). If equipped, ensure
limit switches engage and prevent operation at the required
set point and with drum rotating in correct direction. Ensure
limit switch properly resets.