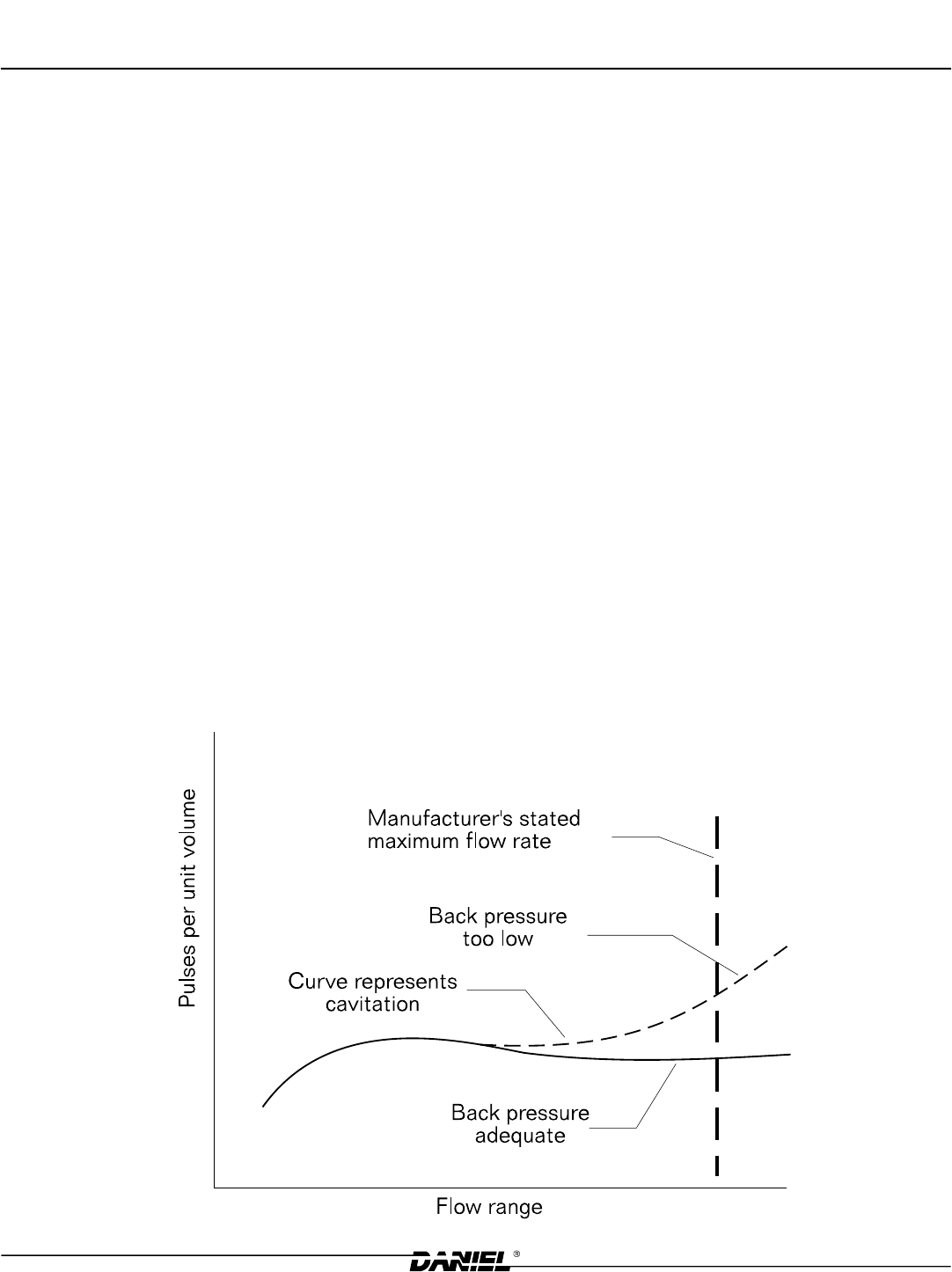
Technical Guide
DAN-LIQ-Turbine Meter-TG-0807
August 2007
Page 18
Figure 14 - Effects of Back Pressure
In some circumstances, the use of a Flow Conditioning Plate (FCP) is possible. The ow conditioning plate is
available from 3” to 6” for the Daniel Series 1500 Liquid Turbine Flow Meter, and is standard on the Daniel
Series 1200 Liquid Turbine Flow Meter (with the exception of the 1”). When supplied, the FCP is an integral
part of the turbine meter. The FCP serves to reduce swirl in the same way as ow straightening sections, and is
of particular signicance where piping installations do not permit long upstream sections, such as in load racks
where space is at a premium.
BACK PRESSURE
It is essential to maintain sufcient back pressure on the turbine meter to prevent ashing and cavitation. This is
particularly important when measuring liquids with high vapor pressures, such as LPGs.
The necessary back pressure required is given by the equation:
BP = (meter ∆P X 2) + (VP X 1.25)
BP = Back pressure required
∆P = Meter pressure drop at maximum flow
VP = Equilibrium vapor pressure of the liquid at the operating temperature, pounds per square inch absolute
(psia), (gauge pressure plus atmoshperic pressure.)
The pulses per unit volume / flow range curves below illustrate the effects of back pressure. Not only does
insufficient back pressure lead to measurement inaccuracy, the resultant flashing and cavitation is extremely
damaging to the flow meter and pipework.